In House Innovation
In 2009, we introduced our first in-house movement: the Breitling Manufacture Caliber 01. Starting from a clean slate, its design was the cumulation of a century-plus of Breitling expertise, and no detail was overlooked. From its functionality and interplay of parts to its aesthetics and ease of servicing, it has become the industry benchmark for chronograph movements. Soon after its release, the exceptional caliber received additional complications, including a GMT function, world-time indication and even a split second—the most difficult chronograph complication in watchmaking.
Our manufacture calibers are subject to painstaking quality control. It takes ten months of production and 1,000 tests to achieve COSC certification. Just as gruelling is our in-house 16-year accelerated aging equivalency for manufacture movements that includes shock testing (approx. 60,000 shocks at 500G), crown testing (more than 100,000 crown winds), winding of the oscillating weight (3,456,000 weight turns) and chronograph pusher testing (approx. 5,840 start-stop-reset engagements). Only once it has passed every test, can a Breitling watch leave the Chronometrie.




Breitling Calibers
Our movements run the gamut from simple time-only three hands to chronograph movements, to calibers with high complications such as the split second, full calendar and tourbillon. We also have non-mechanical calibers, powered by our proprietary SuperQuartz™ technology. To give a sense of the complexity involved in producing a movement, the Breitling Manufacture Caliber 01 alone contains up to 346 components that are carefully assembled and calibrated by hand at the Breitling Chronometrie.
With such labor-intensive production required at the volume of watches we produce, outsourcing some of our entry-level and highly specialized movements allows us to continually meet the demand for our watches at the standards we require. And whether a movement originates at Breitling or is supplied by a partner, every one must achieve COSC certification.
Get to know the entire Breitling caliber family.
The Exclusive Caliber B31
A return to the fundamentals of watchmaking, exclusive time-only Caliber B31 delivers precision and reliability in a sleek, modern form. Only 4.8 mm thick, the movement continues the tradition of in-house innovation established with the Breitling Manufacture Caliber 01, the benchmark for chronograph movements. With the Top Time’s open caseback, there’s a view on the intricate B31 mechanism at work, along with the decorative touches that went into it, including techniques of perlage and Geneva stripes—blending beauty and mechanics.


Manufacture
Although often used interchangeably with “in-house,” manufacture is the more accurate term to describe the top-of-the-line movements engineered by Breitling or co-engineered for Breitling by a highly regarded collaborator. Breitling watches feature both. These include our Breitling Caliber 01-based chronograph complications, the B21 tourbillon chronograph from La Joux-Perret, the B25 full calendar from Concepto and the B20 time-only from Tudor (Kenissi).
These movements undergo rigorous testing to ensure high quality, including a 16-year accelerated aging equivalency. Breitling’s relationship with Tudor is reciprocal, with Tudor supplying components for the B20’s assembly at Breitling, while Breitling supplies the assembled COSC-certified Breitling Caliber 01 for Tudor’s chronograph watches. These collaborations allow Breitling to craft premium timepieces in larger quantities without sacrificing quality.
non-manufacture
non-manufacture


Research & Development
COMBINING CLASSIC WATCHMAKING WITH THE LATEST TECHNOLOGY, BREITLING IS BOTH A COMPANY WITH HISTORY AND ONE THAT’S AHEAD OF ITS TIME. THIS IS THE BRAND THAT INVENTED THE MODERN CHRONOGRAPH, AND TODAY IT MAINTAINS ITS PIONEERING SPIRIT BY CONSTANTLY INNOVATING FROM WITHIN.


Did you know?
We’ve developed our own lubricants for our manufacture calibers, enabling more customized precision and protection of our calibers over the long term. Think of it like an ultra-specialized engine oil for a high-performance vehicle.
Patents
From the modular nature of Breitling’s manufacture movements (that allow for easier assembly, cleaning, and servicing) to revolutionary materials like Breitlight® (a robust material 5.8 times lighter than stainless steel), Breitling’s researchers are responsible for industry-leading advancements. The brand currently holds 25 patents for caliber manufacturing and housings.
Industrialization
Very few other independent watchmakers can produce their own movements at the scale that Breitling does. To meet demand for our watches while providing the highest-quality product, Breitling went back to the drawing board to come up with a seamless assembly method that optimizes workflow between automated tasks and the skilled handcraftsmanship that is the basis of fine watchmaking.


Did you know?
Breitling’s manufacture calibers are constructed on an assembly line that we call the “sushi shop” because, once complete, each piece moves down the line, like at a conveyor-belt sushi restaurant. At the end of this line, all Breitling manufacture calibers are tested in a robotized chronometric station to COSC level—even before they’re sent to COSC.
Homologation
Homologation is a process of quality control and testing based on a set of defined standards. Breitling complies with the NIHS (Normes de l'Industrie Horlogère Suisse) ISO standards and we control for quality according to our own rigorous standards to ensure the precision and longevity of our watches.
FOR ALL WATCHES:
Industry NIHS ISO standard:
• Precision: -4/+6 seconds/day COSC standard (NIHS 95-11)
• Power reserve: Min 60 hours (NIHS 93-20)
• Magnetic protection: 4,800 A/m (NIHS 90-10)
• Shock: 4 shocks at 500G (NIHS 91-10, NIHS 93-20)
• Water resistance: ISO 2281 compliance (NIHS 92-10)
• Chronofiable: Chronofiable® A8, six-month accelerated aging (NIHS 93-20)
Did you know?
Breitling uses an optical camera to precisely quality check the hairspring on the escapement (an object thinner than a human hair).
Did you know?
Breitling’s state-of-the-art laboratory uses such high-tech tools as:
• A robot that tests the chronographs’ start, stop and reset functions
• A scanning electron microscope (SEM) that verifies constructions and analyzes materials
• A high-speed camera that captures high-frequency components, like the chronoworks escapement
FOR MANUFACTURE CALIBERS:
16-year accelerated aging (32 times the Chronofiable® A8 requirement):
• Crown: 100,000 crown winds
• Oscillating weight: 3,456,000 weight turns
• Chronograph pusher: 5,840 start-stop-reset functions
• Case: Salt spray corrosion testing
• Bezel: 2,000 turns
• Dial and strap: 168 hours of UV testing
• Shock: 60,000 shocks at 500G


Swiss Made Quality
All Breitling watches carry the Swiss-made label. This marker of quality and skill is issued to brands that produce their products almost exclusively in Switzerland. Breitling watches are designed, developed, assembled and tested in Switzerland.
MANUFACTURED TO THE HIGHEST STANDARDS, BREITLING WATCHES ARE DESIGNED TO PERFORM IN ANY ENVIRONMENT AND ON ANY MISSION. BREITLING PRODUCED THE FIRST SWISS WRISTWATCH THAT WENT TO SPACE AND WAS A CHOICE OF 007 AGENT JAMES BOND.


Creative Centre
BREITLING’S WATCHMAKERS, CREATORS AND BRAND ARCHITECTS ALL SHARE A PASSION FOR EXCEPTIONAL DESIGN.
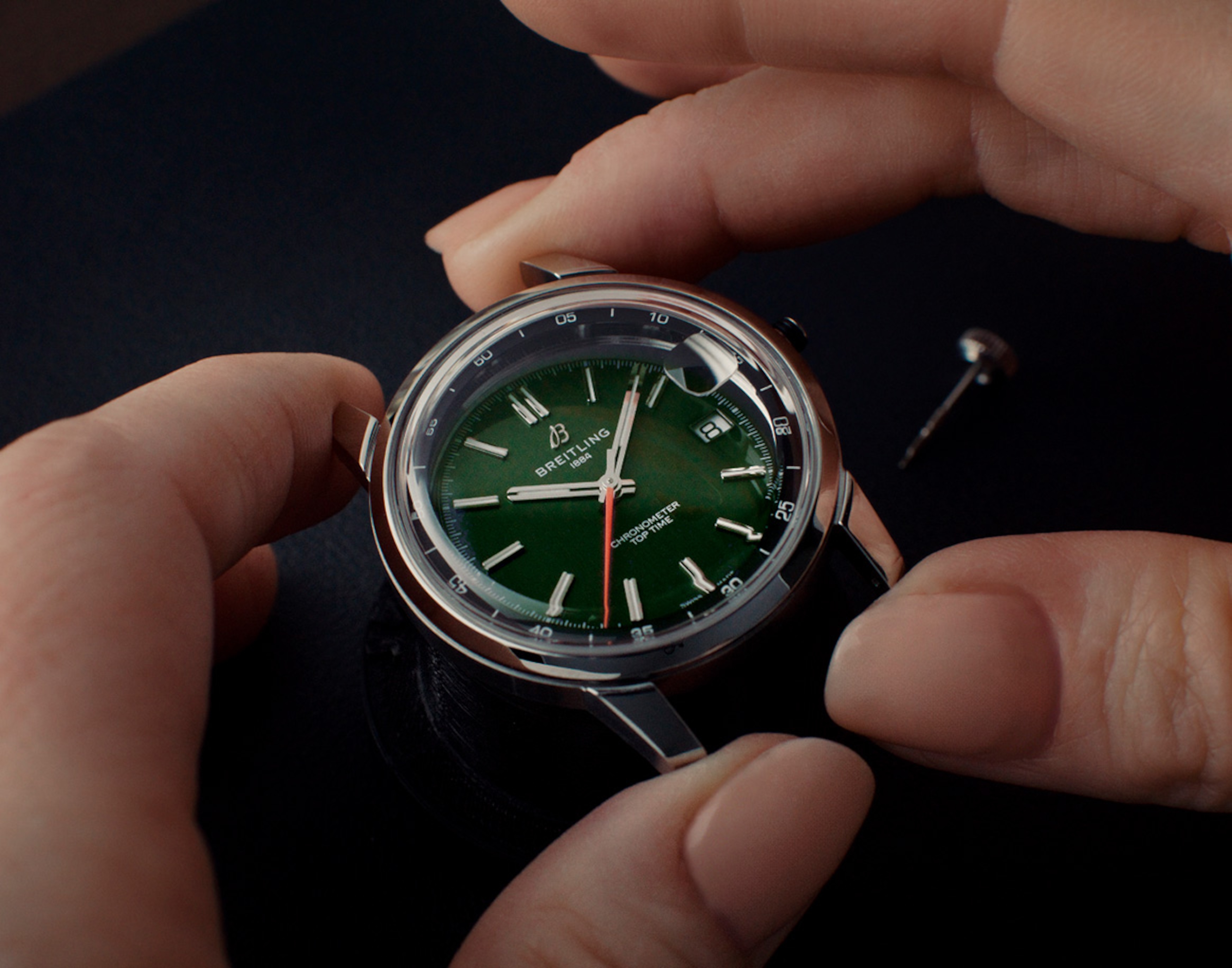
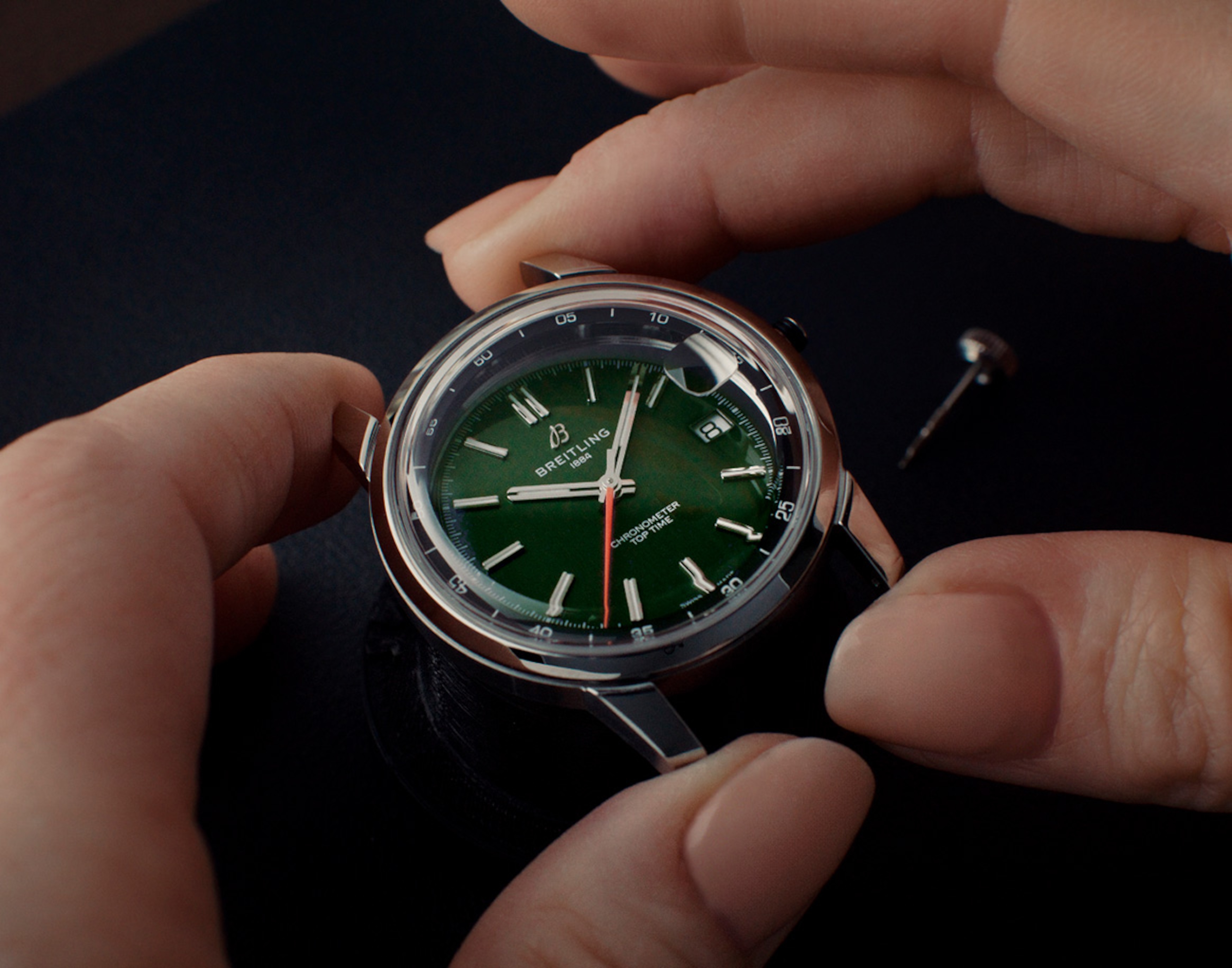
Watchmaking
Breitling employs the industry’s best watchmakers at its Chronometrie, and in service centers around the world. While this art now receives a little help from technology, most of the handcrafted aspects have remained largely unchanged since watchmaking began. Many of our talented professionals come with decades of experience—and some even from families who have been making watches for generations.
Design
Breitling’s design and architect squad have a mission to honor the brand’s century-plus of heritage and legendary name. Our passionate watch designers translate history and emotion into distinctive modern watches. Always pushing the barriers of conventional watch design, they come up with dynamic new directions for our collections. Meanwhile, our brand architects ensure that every Breitling retail space around the world conveys Breitling’s vision of casual, inclusive luxury and feels like a home away from home. From the inviting atmosphere of a Breitling Boutique to the visual appeal of the watch on your wrist, they create an extraordinary Breitling experience.

